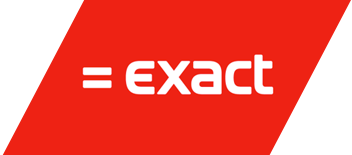
20 apr Materiaalplanning voor voorraadgestuurde productie
Het maakt nogal een verschil of we materiaal plannen voor een voorraadgestuurde productie of voor een ordergestuurde productie. Laten we eerst vaststellen wat we met materiaalplanning bedoelen. De bedoeling van materiaalplanning is om aan de hand van de behoefte aan eindproducten te bepalen welke maakproducten we moeten vervaardigen (werkorders voor eindproducten en halffabrikaten) en welke materialen we moeten inkopen (bestellingen).
Ordergestuurde productie
Er worden eindproducten gemaakt waar een grote variatie in zit. Er kunnen unieke producten bij zitten, maar ook producten die wel vaker worden gemaakt. De gemene deler is dat we ze het liefst niet op voorraad nemen omdat de behoefte slecht te voorspellen is. Daarom maken we er bij voorkeur precies zoveel als besteld door de klant. Voorbeelden van ordergestuurde productie zijn mallen voor spuitgietproducten, verpakkingsmaterialen bedrukt met klantlogo’s, wegwijzers en reclamezuilen. Als er sprake is van halffabrikaten dan zien we het liefst dat die gekoppeld zijn aan de klant. Zo zien we dat alles wat we maken te herleiden is tot een klantorder. In de praktijk komt dit neer op het genereren van suborders. De suborder is een werkorder voor een halffabrikaat, en die suborder levert zijn product aan een ‘hogere’ werkorder. De conventie in Exact Online is dat maakartikelen met de attribuut Ordergestuurd automatisch tot een suborder leiden.
(Klik om te vergroten)
Voorraadgestuurde productie
Er worden eindproducten gemaakt waarvoor regelmatig verkooporders binnenkomen. Van die eindproducten hebben we vaste stuklijsten (recepturen) op basis waarvan we de behoefte aan halffabrikaten en materialen kunnen afleiden. Er kan sprake zijn van halffabrikaten die in meerdere producten gebruikt worden. Evenzo kan het zijn dat het handiger is om de behoefte aan eindproducten te voorspellen in een verkoopprognose in plaats van op de ontvangen verkooporders. Dat is bijvoorbeeld het geval wanneer de productie een langere doorlooptijd heeft dan de orderdoorlooptijd (de drukkerij heeft twee weken nodig om een oplage boeken te drukken, maar de winkel verwacht een levering in twee dagen na order). Voorbeelden van voorraadgestuurde productie zijn levensmiddelen, cosmetica, schroeven en spijkers, autobanden en meubels. In de praktijk betekent dat we zoveel mogelijk de behoefte aan eindproducten, halffabrikaten en materialen samenvoegen per periode (dag, week, of maand) tot een enkele werkorder of bestelling. Daarmee lossen we wel het verband op tussen de klantorder en de werkorder of bestelling. Dus ook het begrip suborder komt te vervallen. Volgens de conventie in Exact Online moeten alle maakartikelen nu de attribuut Voorraadgestuurd krijgen zodat ze niet tot een suborder leiden.
(Klik om te vergroten)
Ordergestuurde en voorraadgestuurde materiaalplanning vergeleken
Stel we hebben twee producten, Eindproduct A en Eindproduct B. Beiden hebben een drielaagse stuklijst: Het eindproduct is laag 0, halffabrikaten K en N zijn laag 1, halffabrikaten L en N zijn laag 2, en er zijn nog wat materialen op laag 3.
(Klik om te vergroten)
Aan de hand van de stuklijsten kunnen we gemakkelijk uitrekenen wat de aantallen zijn van de halffabrikaten en materialen die we nodig hebben om een enkel eindproduct te maken. Dat moeten we natuurlijk voor iedere planningsperiode (dag, week of maand) herhalen zodat de behoefte aan materiaal (te bestellen en te maken) wordt opgesplitst naar de tijd. Op die manier kunnen we het inkopen/maken spreiden en vermijden we de opbouw van te grote voorraden.
(Klik om te vergroten)
Als we nu een order krijgen voor Eindproduct A, dan moeten we met de ordergestuurde methode een werkorder maken voor Eindproduct A, en drie suborders voor halffabrikaten. Ook moeten we vier materialen bestellen. Maar stel nu dat we in week 1 drie orders voor Eindproduct A bestellen en vier in week 2. Dan spreken we nu over 7 werkorders voor A, en 7 x 3 = 21 suborders voor halffabrikaten. Voor de werkvoorbereiding loopt dat snel uit de hand.
Wanneer er dan ook nog orders voor andere eindproducten ontvangen worden met gedeelde halffabrikaten en materialen, dan zijn we beter af met de voorraadgestuurde methode. Nu kunnen we per periode (naar keuze dag, week, of maand) een enkele werkorder per maakproduct of bestelling per materiaal maken. Dat scheelt enorm in werklast voor de werkvoorbereiding. Deze methode heet ook wel Material Requirements Planning, of kortweg MRP.
(Klik om te vergroten)
Waar we in deze uitleg aan voorbijgegaan zijn is het aspect van productie- of besteldoorlooptijd. Natuurlijk moeten we in onze planning daar rekening mee houden zodat de halffabrikaten en productiematerialen gereed zijn wanneer in het hogere niveau de productie aanvangt (bedenk dat het hoogste niveau 0 is, en het laagste niveau het hoogste nummer heeft, dat is nu eenmaal het gebruik in materiaalplanning)
Conclusie
Wanneer we ordergestuurde producten maken zijn we meestal het beste af met het koppelen van werkorders en bestellingen voor materiaal aan de verkooporder (klant). Door te werken met suborders blijft het duidelijk op de werkvloer waar de halffabrikaten voor gebruikt worden.
Wanneer we voorraadgestuurde producten maken kunnen we het beste de productie aansturen met werkorders die de behoefte van een hele periode dekken (week of maand bijvoorbeeld). De behoefte kan bestaan uit meerdere verkooporders of desgewenst een verkoopprognose. Als we willen vermijden dat we te grote voorraden opbouwen en dus alleen voor de aankomende periode willen bestellen en fabriceren, dan is Material Requirements Planning (MRP) de beste oplossing. MRP wordt ondersteund in Exact Online Productie Premium.
Link naar artikel: Klik hier!